The Virtual Microscope - Visualization and inspection of the geometry of simulated particle deposits
The Virtual Microscope - Visualization and inspection of the geometry of simulated particle deposits
Motivation and technical background
Many materials and substances are made of particles from concrete to tablets. Some properties of the finished materials are already strongly determined by the geometric properties of the particle mixtures. In the case of concrete, for example, the space filling of the dry mixture, i.e. the ratio of the container size to the volume of the of the particles contained, is decisive for the strength of the concrete after curing. after curing. In other applications, such as the production of foams, the distribution and shape of the interstices between the between the 'particles', which in this case are voids, play a decisive role in the role in the properties of the material.
The correct choice of the mixture composition or particle size distribution is therefore decisive for the development of particle-based materials with specified properties. Up to now, this has usually required laboratory experiments, but there are successful approaches to at least successful approaches to at least simulate the geometry of the mixtures on the computer. simulate the geometry of the mixtures on the computer. For some years now, the Kolonko group has been developing the RaSim" program system, which simulates the random dense arrangement (packing) of a mixture of k (packing) of a mixture of spherical particles with a given particle size given particle size distribution (KGV). Essential application is concrete research, in which KGVs with the highest possible space high space filling are searched for. As a result the simulation delivers the achieved space filling as a percentage and creates and creates static images of simulated packings with standard software. standard software.
For a use of the simulation in a broader field of application, for example the production of filters and membranes from particles, but also for the production of mixtures for foundry molds or 3D printing, further qualitative properties of the packings must be qualitative properties of the packings have to be determined, which e.g. concern the local interaction of the particles. This is particularly necessary when simulating non-spherical particles, as is already possible in is already possible in some approaches. Here one would like to recognize the relative position of the of the (differently shaped) particles to each other and to assess the to be able to assess the mixing. This would also allow the effects the effects of the individual parameter settings of the simulation, which are simulation, which in turn correspond to real conditions such as pressure or duration of the of the mixing process.
In real under a microscope, it is possible, for example, to study the arrangement and shape of the of the interstices or discover possible (undesired) sorting of the particles. particles. Within the scope of this project a flexible visualization tool that can be used as a kind of virtual microscope allows intensive qualitative investigations of a simulated mixture. This would extend the application spectrum of existing simulation systems, at the same time this would be an important tool for the further development and improvement of the simulation.
State of the art
Particle mixtures
For some fields of application (e.g. concrete or foundry molds), particle size distributions (KGV) are sought which have the highest possible space filling in the dry packing. In the program system RaSim developed in the AG Kolonko, the particles are represented by a random sample of spheres with radii matching the given KGV. From these spheres a 'random close packing' is generated on the computer, which should correspond to a well-mixed real bulk.
Image processing
Graphic aspects are playing an increasingly important role in today's in a wide variety of applications. This ranges from the entertainment sector (video (video and computer games), image processing and 'artificial vision' in (computer vision), for example, in manufacturing automation, to interactive graphical simulations (Virtual Reality, development of virtual prototypes). A central problem in many applications of geometric data is to correctly represent the appearance and position of visible objects. and position of visible objects from large amounts of geometric data, while at the same time the color of the pixels with realistic illumination at the same time. pixels with realistic illumination. The amount of data involved is often so large that it can only be achieved by special algorithms in interaction with the special graphics hardware (graphical processing unit, GPU), realistic images of complex situations in an acceptable amount of time. and also to show the effects of interactive interventions in real time. interactive interventions.
Tasks of investigations
The parallelization of the RaSim simulation system, which is being carried out at the moment, considerably increases the spectrum of possible applications. The results of the simulation must be prepared for the users in a graphical form that is as accessible as possible. They have to be able to inspect the simulated package precisely and to examine it for properties that are important for their application purposes. In this context, a visual impression is much more informative than mere key figures, as they have been available up to now.
At the same time, e.g. due to the more intensive inclusion of non-spherical particles, the demands on the simulation algorithm itself will increase. The core algorithm of iterative collective rearrangement, for example, assumes that the existing overlaps of particles spread evenly over the packing and gradually disappear except for a small, negligible remainder. The actual occurrence of these assumptions, and thus the approximate physical correctness of the simulated arrangements, can best be done with a computer-aided visual examination of the packing.
However, the visualization of the simulation to date has been limited to a simple, offline visualization showing only the exterior of the finished particle packing. Currently, the comparison with the real concrete mix is practically only done by some characteristic values like the space filling, average number of contacts etc..
The Virtual Microscope is expected to provide a significant advance here and, together with the 'virtual stir bar' described below, represent a first step towards a Virtual Particle Laboratory.
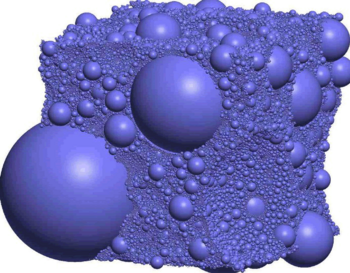
Simple visualization of a concrete mix simulated with RaSim.
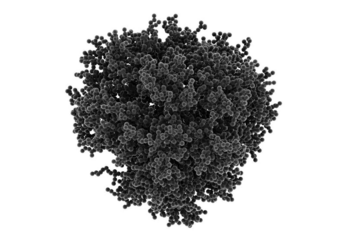
Simulation of an agglomerate of 10,000 similar spheres